This Article Covers Methods Materials And Defects In Plastering Work One By One.
Applying mortar coats on the surfaces of walls, columns, ceiling etc. to get smooth finish is termed as plastering.
Mortar used for plastering may be lime mortar, cement mortar or lime cement mortar. Lime mortar used shall have fat lime to sand ratio of 1: 3 or 1: 4. If hydraulic lime used mix proportion (lime: sand) is 1 : 2. Cement mortar of 1: 4 or 1: 6 mix very commonly used for plastering, richer mix being used for outer walls.
To combine the cost effectiveness of lime mortar and good quality of cement mortar many use lime-cement mortar of proportion (cement : lime : sand) of 1 : 1 : 6 or 1 : 1 : 8 or 1 : 2 : 8.
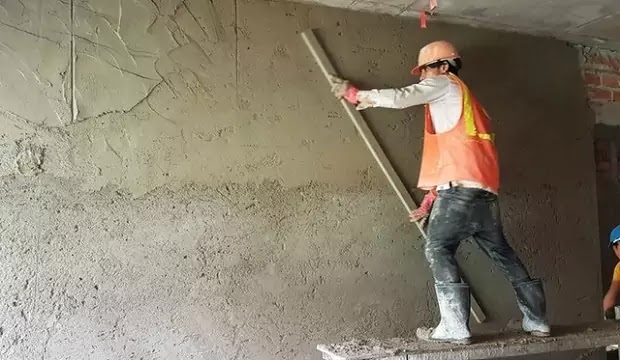
Methods Materials And Defects In Plastering
The objectives of plastering are:-
- To conceal defective workmanship
- To give smooth surface to avoid catching of dust
- For giving good appearance to structure
- To protect the wall from rain water and other atmospheric agencies
- To protect surfaces against vermit.
Requirement of good plaster are:-
- It should adhere to the background easily.
- It should be hard and durable.
- That should prevent penetration by moisture.
- It should be cheap and economical.
- It should possess good workability.
- Should efficiently check entry or penetration of moisture from surface.
Materials For Plastering
Lime mortar usually applied in 3 coats while cement mortar applied in two or three coats for the stone and brick masonry. For concrete surfaces cement mortar may applied in two or three coats. For concrete building blocks many times only one coat of cement mortar applied.The first coat provides means of getting level surface. The final coat provides smooth surface. If three coats used second coat known as floating coat. The average thickness of first coat is 10 to 15 mm. Middle coat thickness is 6–8 mm. The final coat is just 2 to 3 mm thick. If single coat used its thickness kept between 6 to 12 mm. Such coats used on concrete surfaces not exposed to rain. The mortar used for plastering work can be classified into three categories:
Lime Mortar
It consists of equal volume of lime and sand these two materials carefully ground in mortar mill. Flat lime recommended for plastering work.
Cement Mortar
The cement mortar consists of one part of cement to four part of clean, coarse and angular river sand. The materials thoroughly mixed in dry condition before water added to them. The mixing of materials done on a watertight platform.
Water Proof Mortar
This mortar water proof and it prepared by mixing one part of cement and two parts of sand and pulverised alum at the rate of 120 N per m3 sand.
Method Of Plastering
The plastering could done on the surfaces either in one, two and three coats.
The plastering for two coats are as follows:-
- The mortar joints racked out to a depth of 20 mm and surface cleaned and well watered. If it found that the surface to plastered is very rough and uneven, a primary coat is applied to fill up the hollows before the first coat of plaster is put on the surface.
- The first coat of plaster now applied on the surface. The usual thickness of first coat for brick masonry is 9 mm to 10 mm. In order to maintain uniform thickness, the screeds formed on the wall surface by fixing dots.
- The cement mortar placed between successive screeds and surface properly finished. The second coat applied after six hours and thickness of second coat is 3 mm to 2 mm. The completed work allowed to rest for 24 hours and then, the surface kept well
watered for rest of week.
For plastering in three coats are similar to two coats. The thickness of first coat (rendering coat) 9 to 10 mm, second coat (rendering coat) 9 to 10 mm, and third coat (setting coat) thickness around 3 mm.
The techniques for plastering various surfaces
Internal Plastering On Surfaces Of Brick And Concrete:-
Initially, the Surface where plastering to done will be cleaned. Level pegs on walls will fixed with reference to the off lines to brick walls set out in floors. (Using centre plumb bob and nylon thread). All the brick walls will watered before pasting mortar on walls.
First coat mortar filling (1:4 Cement and Sand) up to 15 mm will applied on surfaces where required mortar thickness exceed 25mm. Walls and columns will plastered 1:4 Cement and Sand to achieve semi rough finished surface.
Vertical joint of structural columns / walls & brick walls will treated by fixing 200mm width chicken mesh with wire nails / concrete nails by centering the mesh to the vertical wall joint. All the embedded service lines and provisions (Conduits, Boxes and etc. ) will be completed on brick walls and check with the MEP drawings.
Joints between walls and beams will formed up to a maximum of 20mm and will be sealed using 30 minutes fire rated flexible filler. (Material descriptions will submitted for the approval of the Engineer) Internal plastering on surfaces of concrete columns, beams & walls which aligned with surfaces of brick walls will plastered and other concrete surfaces will finished with cement base easy plaster. (Material descriptions will submitted for the approval of the Engineer).
External Wall Plastering:-
Alignment and fixing level pegs on external wall surfaces will be done using the surveying instrument / centre plumb bobs. Projections on the wall surfaces will chipped off and cleaned after completing the level pegs on walls. First coat mortar filling (1:4 Cement and Sand) up to 15 mm will applied on surfaces where required mortar thickness exceed 25mm.
Cement paste on concrete surfaces will applied to improve the bonding of plaster to the concrete surfaces. Maximum width of 20mm horizontal grooves between walls and beams will formed by cutting using grinders with diamond wheels after plastering the wall surface.
This groove will filled with approved weather sealant. External wall plaster will finished with rough surface. 1:10 slope at the external side of the window sill will formed while plastering the window reveals.
Soffit Plastering / Soffit Finishing With Cement Based Easy Plaster
The slab soffits and beams’ sides and soffits which are to be smooth surfaced painted finished will smoothen with easy plaster (Material literature will submitted separately) and places where concrete surfaces uneven, will roughen & leveled with cement and sand mortar plaster before applying easy plaster to make surface smooth.
- Improving Joints of Brick Wall & Structural Concrete
- 200mm wide Chicken Mesh will fixed at the joint.
- Concrete surfaces will washed and cleaned.
- Concrete surface which are to be plastered will be roughen or put spot cement slurry.
Different Plastering Techniques
There are numerous plastering techniques used to plaster ceilings and walls. It all depends on the requirements of the client as well as the nature of the area that needs plastering. Let’s take a look at some general plastering techniques:
Dry Lining Plastering
Over the years, traditional Melbourne homes made use of wet plastering to ensure a smooth finish to ceilings and walls. During the last 3 to 4 decades, dry plastering or dry lining plastering techniques used instead. This method is favoured due to the ease of using a plasterboard. After all, plasterboards are solid and available in sheet form in standard sizes of around 2.4 x 1.2 meters. Plasterers Melbourne found it a breeze to handle and put plaster on. What is more, dry lining is a complete dry procedure which allow plasterers to quickly fix any mishaps. Paint can easily be applied to any surface to ensure a warm and welcoming finish.
The biggest reason why most builders or plasterers prefer using dry lining is due to the speed of applying it and the load being reduced on structures of any kind. As plasterboard walls are lightweight, they offer better flexibility when it comes to planning interior or exterior spaces on the drawing board. In addition, dry lining is a plastering technique that saves you money and time. Yet another reason why it is the most preferred plastering method as far a construction work in timber frames are concerned.
Wet Plastering
Known to the most common of all plastering techniques used wet plastering. It enables experiences plasterers Melbourne to obtain a clean and smooth finish by covering any surface in need of plastering with mortar, then smoothening it using trowels. Dried wet plastered surfaces can painted or papered according to individual preferences. Like most plastering techniques, it requires skilled plasterers and enough drying time. Wet plastering is prone to shrinkage, cracks, and often times in need of re-plastering in order
to cover any cracks.
Defects In Plastering
The following defects may arise in plaster work.
Blistering Of Plastered Surface
This is the formation of small patches of plaster swelling out beyond the plastered surface, arising out of late slaking of lime particles
in the plaster.
Cracking
Cracking consists of formation of cracks or fissures in the plaster work resulting from the following reasons.
- Imperfect preparation of background
- Structural defects in building
- Discontinuity of surface
- Movements in the background due to its thermal expansion or rapid drying
- Movements in the plaster surface itself, either due to expansion or shrinkage.
- Excessive shrinkage due to application of thick coat
- Faulty workmanship.
Efflorescence
It is the whitish crystalline substance which appears on the surface due to presence of salts in plaster making materials as well as building materials like bricks, sand, cement etc and even water. This gives a very bad appearance. It affects the adhesion of paint with wall surface. Efflorescence can removed to some extent by dry bushing and washing the surface repeatedly.
Flaking
It is the formation of very loose mass of plastered surface, due to poor bond between successive coats.
Peeling
It is the complete dislocation of some portion of plastered surface, resulting in the formation of a patch. This also results from imperfect bond.
Popping
It is the formation of conical hole in the plastered surface due to presence of some particles which expand on setting
Rust Stains
These are sometimes formed when plaster is applied on metal laths
Uneven Surface
This obtained purely due to poor workman ship.
Remedies For Minimizing Defects Plastering Work
- The brickwork and plastering should be carried out in the best workmanship manner.
- The bond of brickwork should maintained properly.
- The efflorescence removed by rubbing brushes on damaged surfaces. A solution of one part of HCl or H2SO4, and five parts of clean water prepared and it applied with the help of brushes on affected area. The surface is washed and cleaned with water.
- The bricks of superior nature should only used for the brick work.
- The water free from salts should used for brick work and plastering work
- The surface to plastered should well watered so that it may not absorb water from plaster.
- The damp- proof courses should be provided at convenient places in buildings.
- The overall construction should be such that the penetration of moisture is prevented.
- The fresh plastered surface should be protected from surplus quantity of water such as rain and excessive heat such as sun.
I Hope You Understand Methods Materials And Defects In Plastering Still Have Any Query”? Fill Free To Comment.
Thank You For Visiting…
Also Checkout Our Video Tutorial Website KPSTRUCTURES.COM
- What is framed structure?
- What is load bearing wall?
- What is earthquake load?
- What is wind load?
- What is live load?
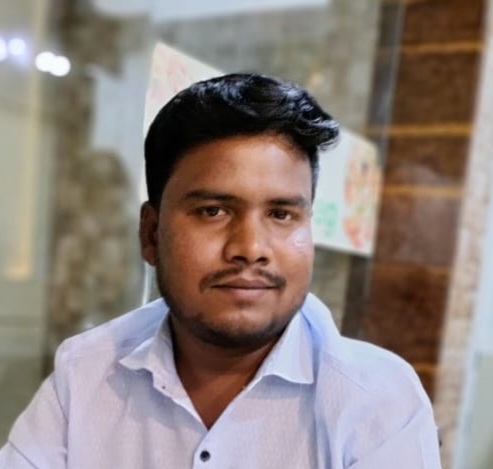
Author & Editor Of This Blog.
Founder Of “KPSTRUCTURES”
Methods Materials And Defects In Plastering Read Again And Query Ask…
6 thoughts on “Guide to Plastering: Methods, Materials, and Defects”