This Article Covers Rail Wear Their Types, Measurements And Method To Reduce Wear One By One.
Rail Wear
Due to the passage of moving loads and friction between the rail and wheel, the rail head gets
worn out in the course of service.
The impact of moving loads, the effect of the forces of acceleration, deceleration, and braking of wheels, the abrasion due to rail-wheel interaction, the effects of weather conditions such as changes in temperature, snow, and rains, the presence of materials such as sand, the standard of maintenance of the track, and such allied factors cause considerable wear and tear of the vertical and lateral planes of the rail head.
Lateral wear occurs more on curves because of the lateral thrust exerted on the outer rail by centrifugal force. A lot of the metal of the rail head gets worn out, causing the weight of the rail to decrease.
This loss of weight of the rail section should not be such that the stresses exceed their permissible values.
When such a stage is reached, rail renewal is called for. In addition, the rail head should not wear to such an extent that there is the possibility of a worn flange of the wheel hitting the fish plate.
Types of Wear on Rails
A rail may face wear and tear in the following positions
(a) On top of the rail head (vertical wear)
(b) On the sides of the rail head (lateral wear)
(c) On the ends of the rail (battering of rail ends)
Wear is more prominent at some special locations of the track. These locations are normally the
following
- On sharp curves, due to centrifugal forces
- On steep gradients, due to the extra force applied by the engine
- And On approaches to railway stations, possibly due to acceleration and deceleration
- In tunnels and coastal areas, due to humidity and weather effects
Measurement of Wear
Wear on rails can measured using any of the following methods
- By weighing the rail
- By profiling the rail section with the help of lead strips
- And By profiling the rail section with the help of needles
- By using special instruments designed to measure the profile of the rail and record it simultaneously on graph paper
Methods to Reduce Wear
Based on field experience, some of the methods adopted to reduce vertical wear and lateral wear in straight paths and curves are as follows
- Better maintenance of the track to ensure good packing as well as proper alignment and use of the correct gauge
- Reduction in the number of joints by welding
- Use of heavier and higher UTS rails, which are more wear resistant
- Use of bearing plates and proper adzing in case of wooden sleepers
- Lubricating the gauge face of the outer rail in case of curves
- Providing check rails in the case of sharp curves
- Interchanging the inner and outer rails
- Changing the rail by carrying out track renewal
Rail End Batter
The hammering action of moving loads on rail joints batters the rail ends in due course of time.
Due to the impact of the blows, the contact surfaces between the rails and sleepers also get worn out, the ballast at places where the sleepers are joined gets shaken up, the fish bolts become loose, and all these factors further worsen the situation, thereby increasing rail end batter.
Rail end batter measured as the difference between the height of the rail at the end and at a
point 30 cm away from the end.
If the batter is up to 2 mm, it is classified ‘average’, and if it is between 2 and 3 mm, it is classified as ‘severe’. When rail end batter excessive and the rail is otherwise alright, the ends can cropped and the rail reused.
Other Effects In Rail
Rail wear and battering of rail ends are the two major defects in rails. However some other types
of defects may also develop in a rail and necessitate its removal in extreme cases.
These as follows:
Hogging of rails

Rail ends get hogged due to poor maintenance of the rail joint, yielding format, loose and faulty fastenings, and other such reasons.
Hogging of rails causes the quality of the track to deteriorate. This defect can be remedied by measured she packing.
Scabbing of rails
The scabbing of rails occurs due to the falling of patches or chunks of metal from the rail table.
Scabbing generally seen in the shape of an elliptical depression; whose surface reveals a progressive fracture with numerous cracks around it.
Wheel burns

Wheel burns caused by the slipping of the driving wheel of locomotives on the rail surface.
As a consequence, extra heat is generated and the surface of the rail gets affected, resulting in a depression on the rail table.
Wheel burns generally noticed on steep gradients or where there are heavy incidences of braking or near water columns.
Shelling and black spots
Shelling is the progressive horizontal separation of metal that occurs on the gauge side, generally at the upper gauge corner.
It is primarily caused by heavy bearing pressure on a small area of contact, which produces heavy internal shear stress.
Corrugation of rail

Corrugation consists of minute depressions on the surface of rails, varying in shape and size and occurring it irregular intervals.
The exact cause of corrugation is not yet known, though many theories have been put forward.
The factors which help in the formation of rail corrugation, however, are briefly enumerated here,
Metallurgy and age of rails
- High nitrogen content of the rails
- Effect of oscillation at the time of rolling and straightening of rails
Physical and environment conditions of track
- Steep gradients
- Yielding formation
- Long tunnels
- Electrified sections
Train operations
- High speeds and high axle loads
- Starting locations of trains
- Locations where brakes applied to stop the train
Atmospheric effects
- High moisture content in the air particularly in coastal areas
- Presence of sand
Thank You For Visiting…
Also Check Video Tutorial Site KPSTRUCTURES.COM
- Understanding the Different Types of Aggregate: A Comprehensive Guide
- Understanding the Different Types of Aggregate in Construction
- Understanding Aggregate: A Comprehensive Guide
- Understanding Standard Tests for Concrete: Ensuring Quality and Durability
- Essential Standard Tests for Concrete: Ensuring Quality and Durability
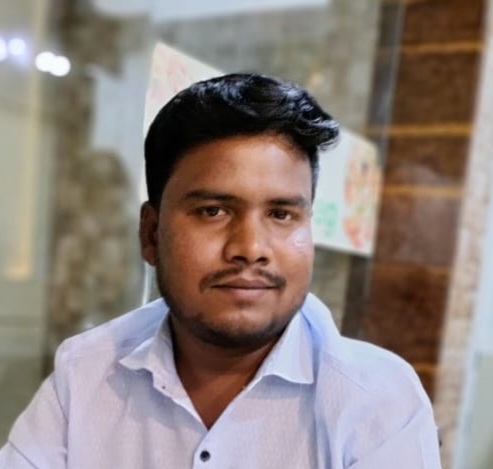
Author & Editor Of This Blog.
Founder Of “KPSTRUCTURES”
2 thoughts on “Rail Wear, Types And Methods To Reduce Wear”