Advancements in High-Performance Concrete: A Comprehensive Overview
Introduction:
Concrete, a ubiquitous construction material, has undergone significant advancements in recent years with the development of High-Performance Concrete (HPC).
HPC is engineered to possess superior mechanical and durability properties compared to traditional concrete, making it an ideal choice for a wide range of applications.
In this article, we will explore the characteristics, composition, production methods, and applications of High-Performance Concrete.

Characteristics of High-Performance Concrete:
Strength and Durability:
High-Performance Concrete is renowned for its exceptional compressive strength, often exceeding 10,000 psi.
This remarkable strength is achieved through a meticulous mix design that incorporates superior quality materials and precise proportions.
Additionally, HPC exhibits enhanced durability, resisting the effects of environmental factors, chemical attacks, and abrasion.
Low Permeability:
One key feature that distinguishes HPC from conventional concrete is its low permeability.
The dense microstructure of HPC minimizes the ingress of water and aggressive chemicals, protecting the reinforcing steel from corrosion.
This characteristic is particularly advantageous in structures exposed to harsh environments, such as marine structures and bridges.
Workability and Flowability:
Despite its high strength, HPC maintains excellent workability, allowing for ease of placement and consolidation.
Innovations in chemical admixtures contribute to improved flowability without compromising the concrete’s overall performance.
This characteristic is especially beneficial in intricate architectural designs and applications with congested reinforcements.
Composition of High-Performance Concrete:
Cementitious Materials:
The choice of cementitious materials is crucial in formulating HPC. High-quality Portland cement, supplementary cementitious materials (such as fly ash and silica fume), and sometimes specialty cements are combined to optimize strength and durability.
The judicious use of these materials contributes to the reduction of heat of hydration and long-term strength development.
Aggregates:
Aggregates in HPC are selected meticulously based on their size, shape, and grading. High-density aggregates, such as crushed quartz or granite, are preferred to enhance the concrete’s overall density and strength.
Well-graded aggregates contribute to improved packing, reducing the void content and enhancing the concrete’s mechanical properties.
Admixtures:
Chemical admixtures play a vital role in the production of HPC.
Superplasticizers are commonly used to improve workability and reduce water content, promoting the flow of concrete without compromising its strength.
Other admixtures, such as air-entraining agents and corrosion inhibitors, are added to tailor the concrete’s properties for specific applications.
Production Methods:
Mix Design:
The mix design of HPC involves a meticulous process to achieve the desired performance. Engineers consider factors such as strength requirements, environmental conditions, and the intended application to formulate a precise mix.
The use of advanced modeling tools and testing methods aids in optimizing the mix design for specific projects.
Quality Control:
Quality control is paramount in the production of HPC. Regular testing of raw materials, including cement, aggregates, and admixtures, ensures consistency and reliability.
Additionally, strict control over mixing, curing, and placement processes is maintained to achieve the desired properties of the concrete.
Applications of High-Performance Concrete:
Bridge Construction:
HPC is extensively used in the construction of bridges due to its high strength and durability.
The ability to withstand heavy loads and resist the corrosive effects of de-icing salts makes HPC an ideal choice for bridge decks and superstructures.
High-Rise Buildings:
The exceptional compressive strength of HPC makes it suitable for high-rise buildings where structural integrity is paramount.
Its low permeability also provides added protection against environmental factors, contributing to the longevity of the structure.
Marine Structures
In marine environments, where structures are exposed to harsh conditions such as saltwater and abrasion, HPC excels. Its resistance to chloride penetration and superior durability make it a preferred material for seawalls, piers, and offshore platforms.
Precast Concrete Elements:
HPC’s high strength and workability make it well-suited for the production of precast concrete elements.
This includes precast panels, beams, and columns, allowing for efficient construction and reduced on-site labor.
Architectural Applications:
The versatility of HPC extends to architectural applications where intricate designs and shapes are desired.
Its ability to maintain high strength while being workable facilitates the creation of aesthetically pleasing structures.
Conclusion:
High-Performance Concrete represents a significant leap forward in the field of construction materials, offering unparalleled strength, durability, and versatility.
The continuous research and development in mix design, production methods, and applications contribute to the widespread adoption of HPC in various construction projects.
As the demand for high-performance structures continues to rise, HPC stands as a cornerstone in the evolution of modern construction materials, paving the way for sustainable and resilient infrastructure.
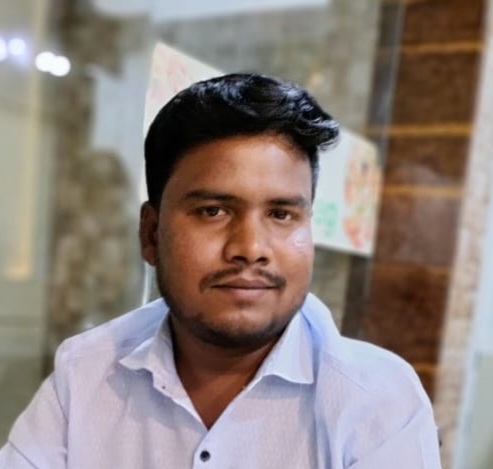
Author & Editor Of This Blog.
Founder Of “KPSTRUCTURES”
2 thoughts on “High performance concrete”