The beam lapping zone is key in construction and manufacturing. It’s important for reinforcement bars that go beyond standard lengths. Engineers must ensure these overlaps work well for load transfer mechanisms.
Knowing how the beam lapping zone works is vital. It helps keep structures strong. This section introduces this important topic. It sets the stage for exploring its role, how to use it, and best practices.
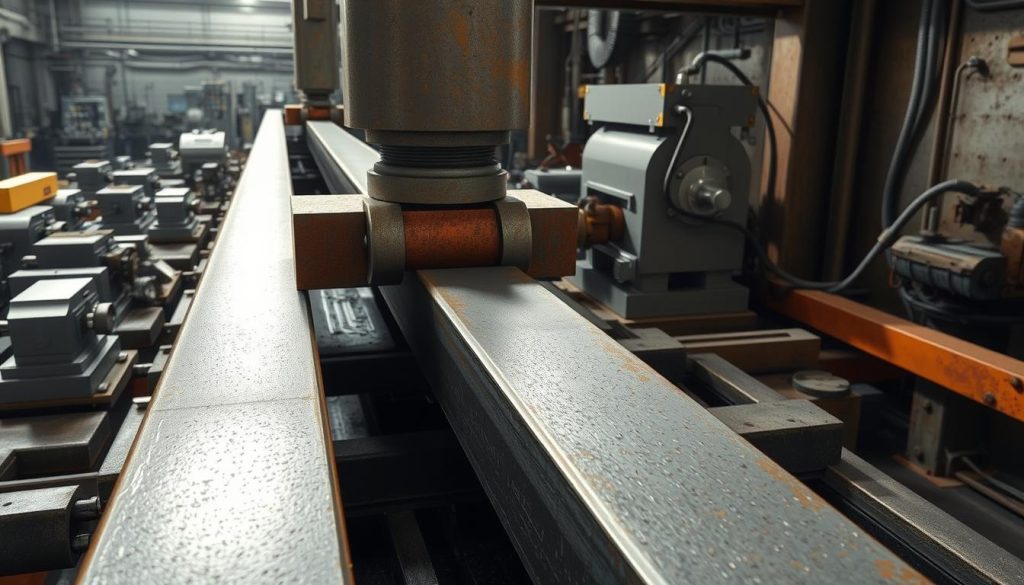
Key Takeaways
- The beam lapping zone plays a vital role in extending reinforcement bar lengths.
- Precision in lap lengths is essential for effective load transfer.
- Structured guidelines help maintain structural integrity in construction.
- Special techniques like mechanical splicing can enhance lapping methods.
- Understanding tension and compression lap requirements ensures safety.
Introduction to Beam Lapping Zone
The beam lapping zone is key in reinforced concrete structures. It helps transfer loads between bars, keeping beams strong. Engineers use special techniques to make these zones work better, reducing the chance of failure.
Reinforcement steel bars are usually 12 meters long, making them easy to move and set up. Each part of a structure has its own rule for how long the lap should be.
For example, the formula to find lap length is Lap Length = 50 x D, where D is the bar’s diameter. Beams and slabs use the same formula, but beams have extra rules for side bars.
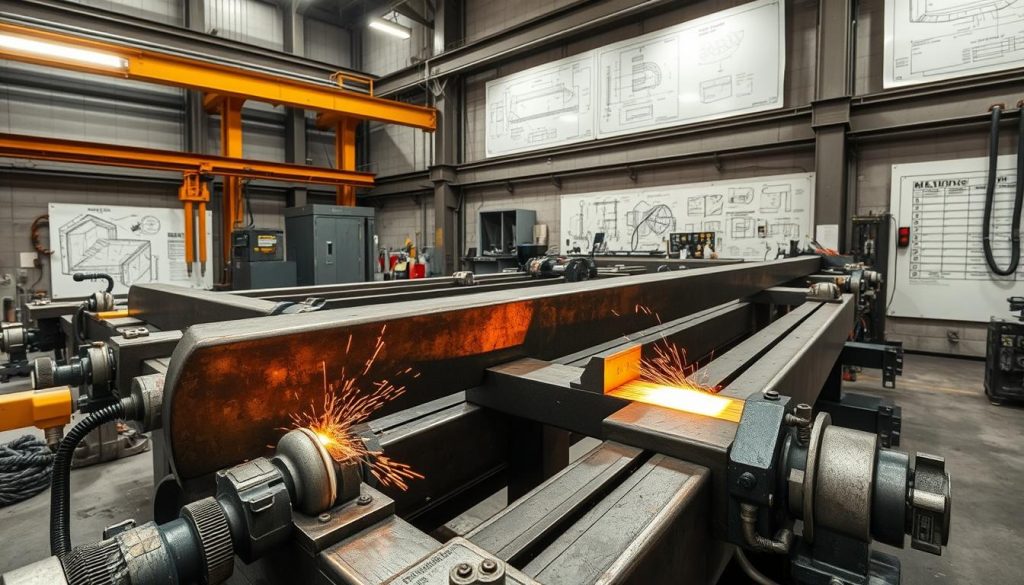
Good design in the beam lapping zone means knowing the difference between lap and development length.
These lengths are important for how well a structure holds up under different loads. The length needed can change based on if the bars are pulling or pushing, usually between 30d to 55d.
Following these rules helps keep beams strong, preventing failures.
In short, understanding the beam lapping zone is vital for safety and reliability in building. By using strong lapping techniques, structural engineers can create lasting and strong structures.
Importance of Beam Lapping in Manufacturing
Beam lapping is key in the manufacturing world. It makes sure that reinforcement bars are well connected. This is vital for the structure’s strength and safety.
Calculating lap lengths is a big deal in making things. For bars under tension, the formula is Lap Length = 50 x D. Here, D is the bar’s diameter.
But, for bars under compression, the lap lengths are shorter. Following these rules helps spread loads evenly, keeping the structure strong.
Beam lapping also saves money. It’s cheaper than old splicing methods. Using mechanical couplers cuts down on costs and makes structures more reliable.
This method is also a safety must. It helps spot and fix weak spots in structures. This way, buildings last longer and stay safe.
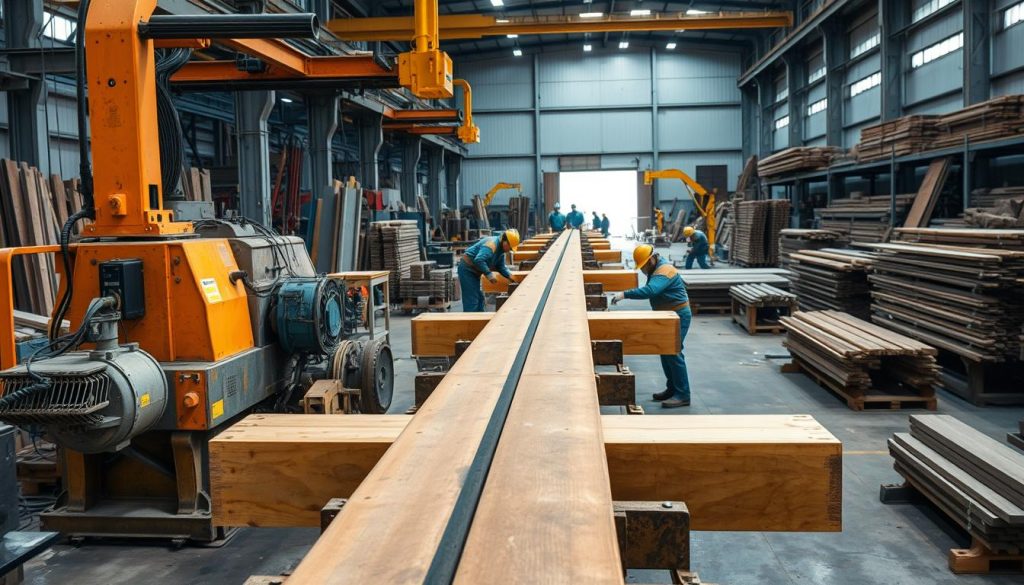
Understanding the Beam Lapping Process
The beam lapping process is key in concrete construction. It makes sure loads are transferred right and structures are strong.
When working with reinforcement bars, there are rules for how to overlap them for the best results. For concrete over 12 meters, lapping is a must, and finding the right lap length is critical.
There are several ways to lap rebar, like contact and non-contact lapping, welding, and mechanical splicing.
Each method has its own needs. For example, non-contact lapping lengths vary from 28 inches to 102 inches, depending on concrete strength.
Contact lapping lengths are usually 1.5 times longer than non-contact, based on the same factors.
Where to lap is also important to avoid stress in structures. It’s best to lap near beams for slabs and close to columns in beam structures. Tension zones need longer lap lengths than compression zones.
Things like staggered lapping, precise placement, bar spacing, and enough concrete cover are vital. Knowing these helps follow manufacturing standards. This ensures buildings are strong and last long.
Learn About Difference Between Load Bearing & Frame Structures
Key Factors in Beam Lapping
Understanding the key factors in beam lapping is key for a stable and durable structure. Load transfer mechanisms and proper reinforcement bar positioning are critical.
These elements affect how loads are spread across the structure, impacting its performance and safety.
Load Transfer Mechanisms
Load transfer mechanisms are vital in beam lapping. They make sure weight and forces move smoothly from one part to another. This keeps the structure strong and intact.
Engineers must carefully plan these mechanisms. This helps avoid stress buildup at the lapping area. It also lowers the chance of the structure failing.
Reinforcement Bar Overlap Positioning
Getting the reinforcement bar positioning right is essential. Bars should not overlap in tension zones. These areas face the highest bending moments.
Instead, overlap should happen in zones with lower bending moments. This approach helps distribute loads better.
It also boosts the structure’s tensile strength and meets building code standards, like those from the American Concrete Institute (ACI).
Identifying Tension Zones in Beams
Understanding tension zones in beams is key to keeping structures strong. Knowing where these areas are helps engineers plan better.
By finding the maximum bending moments, they can place reinforcement bars where they’re needed most.
This approach improves the strength and durability of beams. It’s all about managing stresses effectively.
Defining Maximum Bending Moments
Maximum bending moments happen where loads are heaviest on the beam. This is important for figuring out where to add reinforcement. Tension zones are usually found at mid-span or near supports, based on the load.
Calculating bending moments involves looking at load distribution and support setups. Numerical models help predict how these moments will affect the design.
Evaluating Fiber Stress in Beam Construction
Evaluating fiber stress helps decide where to overlap reinforcement bars. Engineers check tensile and compressive stresses along the beam. For instance, tension zone fibers can see stresses up to 60% of the material’s yield strength.
Getting this right ensures stress is minimal where bars overlap. This boosts performance and reliability.
Using the right methods to calculate these stresses is essential for meeting standards and ensuring safety.
Best Practices for Beam Lapping Zone
Ensuring the beam lapping zone is key for a strong structure. Engineers must focus on even bar overlaps and spacing. This method lowers stress points and boosts the beam’s strength.
A good layout also helps in better load transfer. This makes the beam last longer.
Alternative Levels for Bar Overlapping
IS code rules say no more than 50% of bars should be spliced in beams and columns. If this limit is hit, the lap length must be longer or stirrups must be closer. This keeps the structure strong.
Spacing Considerations for Stirrups in Lapping Areas
Stirrup spacing in lapping areas is vital for stability. Keeping the right distance between stirrups is essential. For big bars, splices should be avoided and welding or mechanical splicing used instead.
Common Lapping Techniques Used in Manufacturing
Knowing common lapping techniques is key for manufacturers looking to improve their work. These methods help make high-quality surfaces, which are vital in many industrial applications. Each technique is designed for different needs in manufacturing.
Some of the most used lapping techniques are:
- Single-side lapping: Great for making one side of a material flat.
- Double-side lapping: Works well for parts that need to be even on both sides, ensuring they are the right size.
- Precision polishing: Used for making surfaces very fine, meeting strict standards.
Many companies use metal lapping services to get the best results. Valley Design, for example, is a leader in precision machining.
They have over 100 machines, from 12” to 64”, handling parts of all sizes and materials. They work with metals like aluminum, copper, and alloys.
These services improve product quality and meet the needs of various industries. This includes telecommunications, aerospace, and medical fields.
Being able to work with different materials helps manufacturers meet different project needs.
In short, using common lapping techniques in manufacturing boosts surface quality and meets industry standards.
With expert metal lapping services, companies can get the precise finishes needed for many industrial applications.
Lapping Technique | Applications | Benefits |
---|---|---|
Single-side Lapping | Precision parts requiring flat surfaces | Cost-effective for large batches |
Double-side Lapping | Optical components, semiconductor wafers | Increased accuracy and efficiency |
Precision Polishing | Medical devices, aerospace components | Achieves ultra-smooth finishes |
Impact of Lapping Length on Structural Integrity
The length of the lap is very important for the strength of beams in building. The right lap length is key to making sure stresses are passed well between reinforcement bars.
If the lap length is too short, it can cause big problems, like in shear walls and columns.
Cautionary Measures for Insufficient Lap Lengths
Short lap lengths mean beams can’t handle loads as well. This can lead to structural failures over time. It’s vital to plan and do things right to avoid stress transfer problems.
Using Eurocode 2 formulas helps find the right lap lengths, considering important factors like the number of bars.
Effects of Lapping on Concrete Cracking
Cracks in concrete can harm the safety and life of structures. Short lap lengths can cause too much stress at joints, leading to cracks.
Studies show that the right lap lengths can lower these risks, making structures perform better under load.
When lap zones are done right, the chance of concrete cracking goes down. This makes the whole structure stronger and safer.
Industrial Lapping Machines: Role and Technology
Industrial lapping machines are key in today’s manufacturing. They improve precision and surface quality.
These machines use advanced technology to get the best results. This helps a lot in making things better in aerospace and car industries.
The demand for aerospace lapping machines is growing fast, at 7.9% each year from 2024 to 2031. The U.S. and Canada are leading, with about 40% of the market.
Europe, with countries like Germany and France, has around 30%. The Asia-Pacific region is growing the fastest, with 25% of the market.
Big names like LAM PLAN, Speedfam, Kemet, and Barnes Aerospace use lapping tech for top-notch finishes.
For example, LAM PLAN makes about €30 million, and Speedfam makes around $40 million. They use different lapping methods to meet strict standards.
These machines are used in many ways and work efficiently. Vertical lapping machines are great for precise jobs, like making gauge blocks and ball bearings.
Centerless lapping machines get amazing finishes, sometimes as fine as 0.05 microns. Spherical lapping machines are for round objects, and belt lapping uses a cloth belt to remove material.
Precision Lapping and Surface Finishing
Precision lapping is key to making products better and more reliable. It helps create smooth surfaces, vital in aerospace and automotive. This process makes components last longer and work better.
Abrasive films are essential for surface finishing. They are used in many fields, like medicine and electronics. In making semiconductors, they help achieve ultra-smooth surfaces. This ensures components perform well.
New tools in surface finishing have made things better. They make the process more efficient and effective. This is good for industries like machinery and marine, where precision is critical.
Valley Design is a leader in precision lapping and polishing. They have over 50 years of experience. Their machines can handle all sorts of lapping needs, meeting high quality standards.
In short, precision lapping and surface finishing are vital in making products better. They show a move towards more precise and efficient manufacturing.
Beam Lapping Zone: Engineering Guidelines
The beam lapping zone is key in reinforced concrete design. Following engineering rules keeps structures strong under different loads. Making sure the lap length is right is very important for reinforcement to work well.
In tension areas, the lap length for steel bars is 50 times the bar’s diameter. For a 16mm bar, that’s 800mm.
In compression areas, it’s 40 times the diameter, so 640mm for the same bar. This shows we need to adjust lap length based on stress in the beam lapping zone.
- Staggered Lapping: This method staggers lapping points in multi-story buildings. It improves reinforcement and avoids weak spots.
- Adequate Spacing: Keeping bars spaced right ensures good load transfer and concrete bonding.
- Concrete Cover: Enough concrete cover over steel bars stops corrosion. This keeps the structure strong and durable over time.
- Special Lapping Techniques: When regular lapping doesn’t work, mechanical splicing and welding are good alternatives for joining steel bars.
By sticking to these guidelines and understanding the beam lapping zone, builders can steer clear of problems. This ensures the structure’s integrity and success throughout its life.
Conclusion
The beam lapping zone is key to making structures reliable in manufacturing. By looking at things like lap splice lengths and where to put PZT transducers, we learn a lot.
This knowledge helps us monitor and analyze reinforced concrete beams better.
Studies show that longer lap lengths can handle more load and reduce mid-span deflection. This is important for engineers who want to build strong and lasting structures.
Using new technologies like wave propagation helps find damage early and keeps projects going longer.
Beam design is complex, so finding new ways to monitor them is critical. This keeps structures safe and sound.
The beam lapping zone conclusion is more than just a summary. It encourages us to keep improving our engineering methods to meet new challenges.
FAQ
What is the beam lapping zone?
The beam lapping zone is where reinforcement bars overlap in concrete structures. This is key for transferring loads between bars, ensuring the structure stays strong.
Why is beam lapping important in construction?
It’s important because it lets bars extend, making structures stronger. Good lapping helps distribute loads well, reducing failure risks.
How does the beam lapping process work?
The process overlaps bars at specific points. This creates a continuous length, helping to distribute loads and prevent concrete cracks.
What are the key factors to consider in beam lapping?
Important factors include how loads are transferred and where bars overlap. Proper placement is key to maintaining strength and preventing issues under heavy loads.
How do you identify tension zones in beams?
Tension zones are found where bending moments are highest. Engineers use this to place bar overlaps in low-stress areas.
What are best practices for managing the beam lapping zone?
Best practices include using different levels for overlaps and ensuring stirrups are spaced right. This boosts stability and load-carrying ability.
What are common lapping techniques used in manufacturing?
Manufacturing uses various lapping methods for different needs. Metal lapping services focus on achieving top-notch finishes and quality.
How does lapping length affect structural integrity?
Lap length is vital for structural integrity. Short laps can cause stress, leading to cracks and weakening the structure.
What role do industrial lapping machines play in manufacturing?
Industrial lapping machines make manufacturing more efficient. They ensure high-quality finishes and precise tolerances, improving production.
Why is precision lapping important in surface finishing?
Precision lapping is key for top-notch finishes and quality. It’s vital in advanced manufacturing, like in aerospace and automotive.
What engineering guidelines should be followed in the beam lapping zone?
Guidelines include best practices and standards for lapping. They ensure structures stay strong throughout their life.
- What is framed structure?
- What is load bearing wall?
- What is earthquake load?
- What is wind load?
- What is live load?
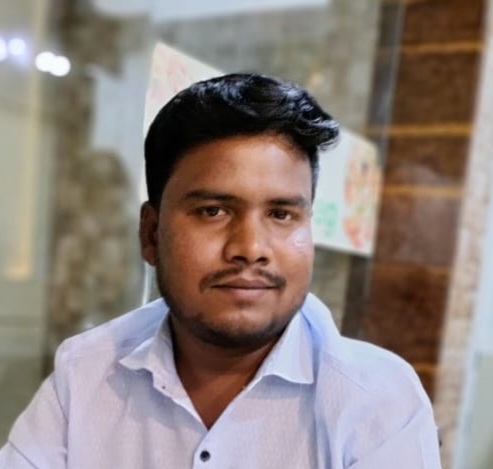
Author & Editor Of This Blog.
Founder Of “KPSTRUCTURES”
2 thoughts on “Understanding Beam Lapping Zone in Manufacturing-2025”