Slow set refractory mortar is a special material that can handle very high temperatures. It’s used in places like steel factories and furnace buildings.
This mortar is made with refractory cement, which is great at staying strong even when it’s hot.
Calcium aluminate cement is a key part of this mortar. It makes the mortar stronger and more durable than regular cement.
This is why slow set refractory mortar is so important for keeping things stable in very hot places.

Key Takeaways
- Slow set refractory mortar is a high-temperature resistant material used in industrial applications.
- Refractory cement, such as calcium aluminate cement, offers excellent hydration capacity and high refractoriness.
- High temperature mortar, like slow set refractory mortar, is essential for withstanding extreme temperatures.
- Slow set refractory mortar provides superior strength and durability compared to ordinary Portland cement.
- The use of slow set refractory mortar can help maintain structural integrity in high-temperature environments.
- Refractory mortars, including slow set refractory mortar, are used in various applications, including steel production and furnace construction.
- Slow set refractory mortar is a critical component in high-temperature applications, providing a reliable and durable solution.
Understanding Slow Set Refractory Mortar
Slow set refractory mortar is made to handle high temperatures. It’s perfect for fireplaces, furnaces, and more. It uses special cement and aggregates for heat and durability.
Silica sand is used because it has sharp grains for better grip. The water should be between 10ºC to 25ºC for mixing. Proper mixing and curing techniques are key for the best results.
What Makes Refractory Mortar Different
Refractory mortar stands out because it can handle high temperatures. It uses heat resistant mortar and fireproof mortar for this. It’s also more durable and long-lasting, making it a favorite for many.

The Science Behind Slow Setting Properties
The slow setting of refractory mortar comes from chemical reactions. Calcium aluminate cements and high-temperature-bearing aggregates slow down the setting.
This makes the mortar more workable and durable. It’s also flexible to reduce cracking and damage.
Essential Properties of Heat Resistant Mortar
In industrial settings, industrial mortar is key for handling high temperatures. A refractory material is vital, as it can handle temperatures up to 2,550°F. Regular mortars can only go up to 600°F.
A strong mortar is needed for the structure’s durability and to resist thermal shock. Using refractory materials in industrial settings offers many benefits. It can handle extreme temperatures and stay strong.
Heat-resistant mortar has several important qualities. It can handle high temperatures, is strong, and durable. Here are some key features of heat-resistant mortar:
- Withstands elevated temperatures up to 2,550°F
- Meets ASTM C-199 standards for mortar temperature limits
- Resists high temperatures for a minimum of 6 hours

Heat-resistant mortar also has economic benefits. Using industrial mortar and refractory materials can lower maintenance costs. It also helps extend the structure’s life.
Property | Value |
---|---|
Maximum service temperature | 2,600°F (1,427°C) |
Compressive strength | 3,500 psi (246 kg/cm²) |
Flexural strength | 800 psi (56 kg/cm²) |
Applications and Uses in Industrial Settings
Slow set refractory mortar is a key material in many industrial settings. It’s used in high-temperature manufacturing, furnace and kiln construction, chemical plants, and power generation. Its high-temperature and corrosive resistance makes it perfect for these jobs.
In high-temperature manufacturing, it lines furnaces and kilns. This protects them from extreme heat and chemical damage. High temperature mortar keeps the equipment running well and lasting longer.
Some of the main uses of slow set refractory mortar are:
- Furnace and kiln construction
- Chemical processing plants
- Power generation facilities
- High-temperature manufacturing facilities
Refractory concretes, like slow set refractory mortar, are vital in many industries. These include refractories, metallurgical, and cement.
They help in high-temperature settings, boosting efficiency, cutting down on maintenance, and making things safer.
Industry | Application | Benefits |
---|---|---|
Refractories | Furnace lining | High-temperature resistance, corrosion protection |
Metallurgical | Kiln construction | Efficient heat transfer, reduced energy consumption |
Cement | High-temperature manufacturing | Improved product quality, increased productivity |
Advantages of Using Slow Set Refractory Mortar
For high-temperature jobs like fireplaces, fireproof mortar is key. Slow set refractory mortar stands out because it can handle very high temperatures. It also has great strength and lasts a long time, making it reliable.
Slow set refractory mortar has many benefits. Here are a few:
- It can handle very high temperatures, perfect for heat resistant mortar jobs.
- It’s very strong and durable, lasting a long time.
- It’s flexible and can adapt to changes in construction.
Also, slow set refractory mortar works well with different stones. This makes it great for stone masonry.
Its special properties make it a top choice for fireproof mortar and heat resistant mortar projects.
Property | Description |
---|---|
Temperature Resistance | Up to 2,550°F |
Compressive Strength | Optimized through factory-controlled admixture addition |
Flexibility and Adaptability | Allows it to withstand movement and deflection in construction |
Installation Techniques and Best Practices
Installing industrial mortar right is key to its best performance and lasting use. First, the surface must be cleaned and prepared.
This step is vital for a strong bond between the mortar and the material. Next, mixing and applying the mortar must follow the manufacturer’s guide for the right consistency and strength.
The curing and setting of strong mortar are also very important. The best temperature for curing is between 70°F to 90°F. Curing below 70°F can lead to weaker material, lower permeability, and longer curing times.
Remember, the critical temperature for removing free water is 212°F (100°C), and dehydration temperatures for cement phases range from 440°F to 1020°F.
To ensure a good installation, follow these best practices:
* Use a mixing ratio of bricks as close to 1:1 as possible.
* Make sure at least one corner of the brick touches the kiln shell.
* Use 2 mm (1% of brick length) cardboard spacers in radial joints.
* Fill gaps from welding seams or deformations with mortar.
These steps help avoid poor lining quality and ensure a strong, durable refractory material.
Comparing Different Types of Fireproof Mortars
There are many types of fireproof mortars, like slow set refractory mortar, refractory cement, and high temperature mortar.
Each has its own special features and benefits. For example, slow set refractory mortar can handle very high temperatures and is often used in industrial places.
Refractory cement is made to stand up to extremely high temperatures. It’s perfect for furnaces and kilns. High temperature mortar is used for fireplaces and chimneys because it can handle high heat.
The main differences are in what they’re made of, how well they conduct heat, and their density. Perlite and vermiculite are often used because they don’t conduct heat well and don’t melt easily.
Slow set refractory mortar is great for industrial projects, like furnaces and kilns. Refractory cement is used for fireplaces and chimneys.
High temperature mortar is best for high-temperature equipment, like boilers and heat exchangers.
Maintenance and Longevity Considerations
Keeping fireproof mortar, heat resistant mortar, and mortar for fireplaces in good shape is key. Regular checks are important to catch problems early. Look for cracks, gaps, and wear and tear.
Small problems with these mortars can often be fixed with a bit of effort. For instance, small gaps can be sealed with refractory caulk. But bigger issues might need a pro.
Extending Service Life
To make these mortars last longer, follow the right steps when installing and maintaining them. Use the right materials, like stainless steel fibers. Also, make sure the mortar is cured and set correctly.
The cost of these materials can be high, from $150 to $500 per metric ton. But, they can last from 1 to 10 years, with an average of 5. Using refractory instead of steel can save money over time, from $900 to $3,000 in 30 years.
Material | Cost per Metric Ton | Lifespan |
---|---|---|
Refractory | $150-$500 | 1-10 years |
Steel | $800-$850 | 1 year |
By taking good care of these mortars and using the right materials, they can last longer. This means less need for repairs and replacements.
Safety Considerations and Environmental Impact
Working with industrial mortar, refractory material, and strong mortar needs careful thought about safety and the environment.
It’s important to handle and dispose of these materials properly. This helps reduce harm to the environment. Industries using refractory concretes must focus on mixing and curing right to get the best results.
Wearing personal protective equipment (PPE) is a must to avoid health problems. It’s also vital to watch the environmental effects of cement kilns and how they handle hazardous waste. Here are some main points to think about for safety and the environment:
- Proper handling and disposal of industrial mortar and refractory materials
- Use of PPE to prevent health risks
- Monitoring and regulation of cement kilns and co-processing of hazardous wastes
Putting safety and the environment first helps make the use of industrial mortar, refractory material, and strong mortar better. This way, we can reduce risks and work towards a greener future.
Material | Safety Consideration | Environmental Impact |
---|---|---|
Industrial Mortar | Proper handling and disposal | Monitoring of cement kilns |
Refractory Material | Use of PPE | Regulation of co-processing of hazardous wastes |
Strong Mortar | Attention to mixing and curing techniques | Minimization of environmental impact |
Cost Analysis and Return on Investment
Thinking about using slow set refractory mortar, refractory cement, or high temperature mortar? It’s key to look at the costs and what you’ll get back. These materials might cost more upfront than usual, but they last longer and work better.
Calcium aluminate cement, a main part of refractory mortar, costs more than regular cement. But it’s worth it because it handles high heat well, works well in wet places, and lasts a long time.
Using slow set refractory mortar, refractory cement, or high temperature mortar saves money in the long run.
They can handle very hot temperatures and harsh environments. This means you won’t have to fix or replace them as often.
Material | Initial Cost | Long-term Benefits |
---|---|---|
Slow Set Refractory Mortar | Higher initial cost | Reduced maintenance costs, extended service life |
Refractory Cement | Higher initial cost | High refractoriness, excellent hydration capacity |
High Temperature Mortar | Higher initial cost | Withstands extreme temperatures, reduces maintenance costs |
In summary, even though slow set refractory mortar, refractory cement, or high temperature mortar cost more to start, they’re a smart choice.
They offer long-term benefits and save you money on upkeep for industries needing to handle high heat and last a long time.
Conclusion: Making the Right Choice for Your Refractory Needs
Slow set refractory mortar is great for high-temperature jobs. It’s very heat resistant and lasts a long time. Plus, it’s easy to use and saves money.
If you need to build a new furnace or fix an old kiln, this mortar is perfect. It’s made with special materials for top performance. It keeps your structures strong, even in tough conditions.
FAQ
What is the difference between slow set refractory mortar and other types of mortar?
Slow sets refractory mortar is made for high heat, perfect for fireplaces and industrial use. It has calcium aluminate cement for strength and lasts longer than regular mortars.
What are the key components of slow set refractory mortar?
It has calcium aluminate cement, silica, and other materials. The slow setting comes from its special mix.
What are the essential properties of heat-resistant mortar?
It needs to be strong, last long, and handle heat well. This is key for places that get very hot.
Where is slow sets refractory mortar commonly used in industrial settings?
It’s used in places that get very hot, like factories and power plants. It can handle high temperatures and harsh environments.
What are the advantages of using slow set refractory mortar?
It resists high heat, is strong, and lasts a long time. This makes it great for fireplaces and other hot spots.
What are the best practices for installing slow set refractory mortars?
You need to prepare the surface right, mix and apply it correctly, and let it cure properly. This ensures it works well.
How does slow set of refractory mortar compare to other fireproof mortars?
It’s chosen for its heat resistance, strength, and durability. It’s a top pick for many high-temperature jobs.
How can I ensure the longevity of my slow set refractory mortars installation?
Keep it maintained by checking it often, fixing issues, and following best practices. This helps it last longer.
What are the safety and environmental considerations when using slow set refractory mortar?
Always follow safety rules and handle it carefully to avoid harm. Dispose of it properly to protect the environment.
How can I evaluate the cost-effectiveness of using slow set refractory mortar?
Look at the upfront cost, long-term savings, and maintenance costs. Its durability and performance can save money over time.
- The Importance of Concrete in Construction
- Understanding the Properties of Concrete: A Comprehensive Guide
- Understanding the Key Properties of Concrete
- Exploring the Versatile Uses of Concrete in Everyday Life
- Understanding Concrete Classification: A Comprehensive Guide
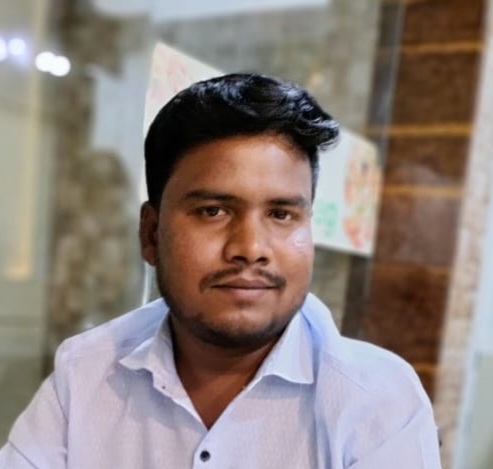
Author & Editor Of This Blog.
Founder Of “KPSTRUCTURES”