Off-site construction, also known as prefabricated building or modular construction, is becoming more popular. It offers many benefits.
For example, it can cut construction time by up to 50% compared to traditional methods.
It also makes work safer for workers and ensures higher quality. This leads to better assurance of quality in construction projects.
Off-site construction can save money too. It uses advanced technologies that help reduce environmental impact.
Projects can also see faster delivery times, lower costs, and better health and safety.
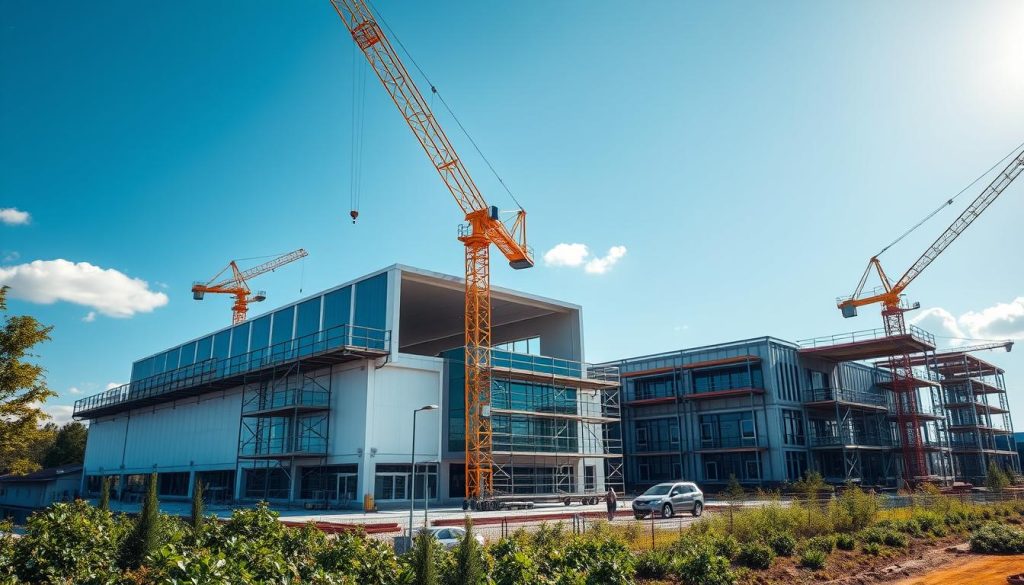
Off-site construction is changing the construction industry for the better. It brings many advantages that can make projects more efficient and of higher quality.
By understanding these benefits, construction companies can make better choices and improve their work.
Key Takeaways
- Off-site construction can reduce construction time by up to 50% compared to traditional building methods.
- Off-site construction provides safer working conditions, reducing worker exposure to hazards.
- Improved quality control in off-site construction environments leads to a higher degree of quality assurance.
- Off-site construction can deliver cost savings through better labor rates and productivity.
- Using advanced technologies for prefabrication can significantly reduce environmental impact.
- Off-site construction offers faster delivery times, up to 30% lower costs, and better health and safety.
Understanding Off-Site Construction Fundamentals
Off-site construction, or offsite manufacturing, means making building parts or whole modules in a factory.
Then, they are moved to the building site for assembly. This method is becoming more popular because it can make construction more efficient, cut down on waste, and improve quality.
Using modular buildings and construction offsite methods can greatly improve productivity. It reduces the need for workers on site and lowers the environmental impact of building.
By using offsite manufacturing, builders can make their work flow better, save money, and finish projects quicker.
Defining Modern Off-Site Construction Methods
Today’s off-site construction uses advanced tech like Building Information Modeling (BIM) and virtual design and construction (VDC).
These tools help design and make building parts. They allow for detailed digital models that help plan construction, spot problems, and improve building performance.
Key Components of Off-Site Manufacturing
The main parts of off-site manufacturing are prefabricated modules, panelized construction, and modular buildings.
These are made in a factory, where they can be made more precisely and with better quality than building on site.
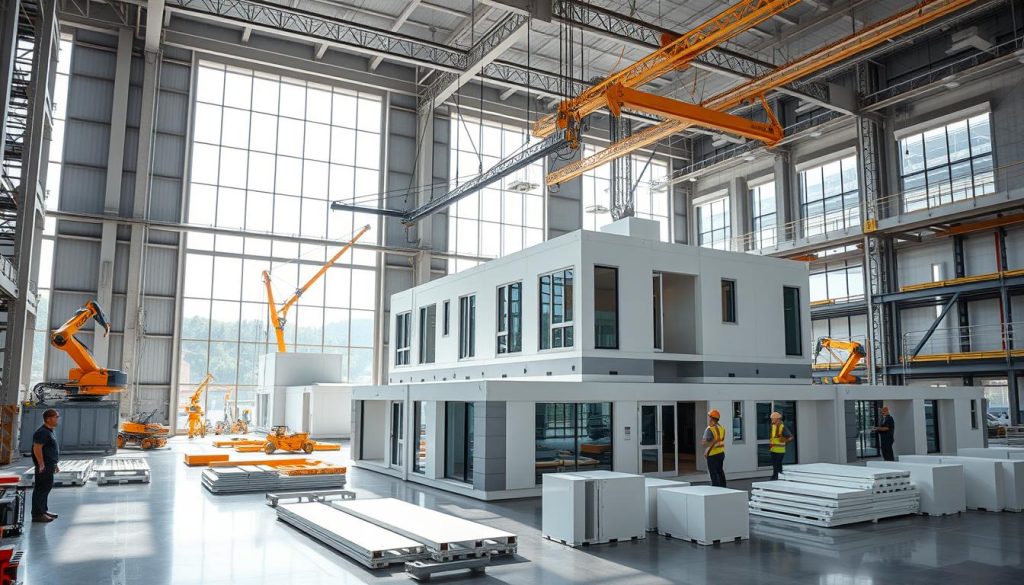
Evolution of Construction Technology
The growth of construction technology has helped develop off-site construction methods. New digital design tools, automation, and robotics have made construction more efficient and productive. This allows for the creation of building parts and their assembly on site.
Benefits of Off-Site Construction | Description |
---|---|
Improved Quality Control | Enhanced quality control processes lead to higher standards of finished projects |
Reduced Waste | Minimized material waste contributes to more sustainable building practices |
Increased Efficiency | Streamlined workflows and reduced onsite manpower lead to faster project completion times |
The Economic Impact of Prefabricated Building Solutions
Prefabricated building solutions, like modular construction and panelized construction, bring big economic wins.
They cut down on construction costs and boost productivity. Studies show, the modular construction market can save up to 20% compared to old-school building methods.
Some major economic pluses of prefabricated building solutions include:
- Lower labor costs: up to 20% thanks to the factory setting
- Quicker project finish: weeks to months, unlike traditional projects that take months or years
- Smaller financing costs: quicker projects mean lower loan costs for investors
Also, prefabricated building solutions cut down on waste and lower energy costs over time. This makes building more sustainable.
With the prefabricated construction market set to grow, thanks to tech advancements, these solutions are key to the future of building.
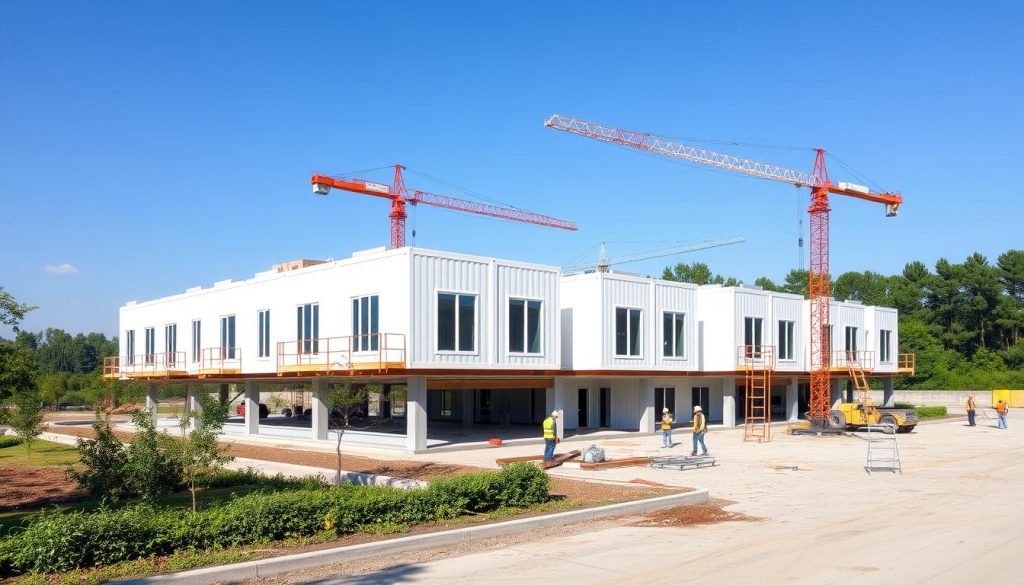
Essential Components of Modular Construction Systems
Modular construction means building parts of a project off-site. These parts are complete units with walls, floors, and more. It’s great for projects that need lots of the same thing, like apartments, hotels, and student housing.
For modular construction to work, you need to put together structural parts, materials, and MEP systems.
Quality control processes are key to making sure everything is safe and up to standard. About 80% of modular work happens off-site, showing how important clear communication is.
Modular construction has many benefits, including:
- Cost savings of up to 10% compared to traditional on-site construction
- Faster completion times, typically taking two to four months to complete
- Reduced waste and environmental impact
Modular buildings follow the same rules and use the same materials as regular buildings. This shows a big change towards building in factories instead of on-site.
Construction Method | Completion Time | Cost Savings |
---|---|---|
Modular Construction | 2-4 months | Up to 10% |
Traditional On-Site Construction | 6 months to 1 year | N/A |
Time Management Benefits in Off-Site Manufacturing
Off-site construction brings many time-saving benefits. It cuts down construction time and boosts productivity.
Companies can work on many projects at once, making their workflow better and reducing delays. They also use resources more wisely because they need less on-site labor.
Some key advantages of off-site construction include:
- Modular and off-site manufacturing can cut construction time by up to 50% compared to traditional methods
- Projects using off-site manufacturing see a 20% to 30% boost in labor productivity
- Off-site construction avoids weather delays, letting projects go on all year in a controlled setting
Remote construction and offsite manufacturing also help streamline processes. They cut down on manual errors and make reporting better.
With manufacturing software, companies can see their projects clearer, save on materials, and cut waste. Adopting off-site construction boosts efficiency, lowers costs, and makes customers happier.
The time-saving perks of off-site manufacturing make it a great choice for companies wanting to be more productive and efficient.
By using off-site construction, companies can stay ahead in the market and deliver top-notch projects on time and within budget.
Benefit | Description |
---|---|
Reduced Construction Time | Up to 50% reduction in construction time compared to traditional methods |
Improved Productivity | 20-30% increase in labor productivity |
Eliminated Weather-Related Delays | Construction projects can proceed year-round in a controlled environment |
Environmental Advantages of Remote Construction
Remote construction, also known as offsite manufacturing, has many environmental benefits. It lets builders create modular buildings in a factory.
This way, they can focus on sustainability. It’s a great choice for those wanting to cut down on their carbon footprint.
Some key environmental benefits include:
- Reduced carbon footprint: Offsite manufacturing cuts down on transportation and on-site work. This leads to lower greenhouse gas emissions.
- Waste minimization: Using precision cutting and reusing materials greatly reduces waste. This makes remote construction more eco-friendly.
- Sustainable material usage: Modular buildings can use sustainable materials. This lowers the environmental impact of building them.
The U.S. Census Bureau says only three percent of single-family homes are built this way. But, this number is expected to rise.
Thanks to offsite manufacturing and modular buildings, the construction industry can be greener. It can also provide quality, sustainable homes.
Environmental Benefit | Description |
---|---|
Reduced Carbon Footprint | Lower greenhouse gas emissions due to reduced transportation and on-site construction |
Waste Minimization | Precision cutting and material reuse reduce waste and costs |
Sustainable Material Usage | Modular buildings can be designed to incorporate sustainable materials, reducing environmental impact |
Quality Assurance in Offsite Building Methods
Quality assurance is key in offsite building, like modular and prefabricated construction. It makes sure all parts are made just right. This leads to better assembly and fewer mistakes.
Some benefits of quality assurance in offsite building methods include:
- Reduced contamination risks
- Enhanced worker safety and productivity
- Improved assembly precision
- Uniformity and accuracy in component production
Offsite construction goes on all year, no matter the weather. Factories cut down on contamination risks. Workers are safer and more productive in controlled environments. Computer-Aided Design (CAD) makes sure every part is made to the exact right specs.
Regular checks during making can find problems early. This means less waste and fewer mistakes at the building site. The end result is a more precise and consistent final product.
Using new tech like CAD and laser scanning boosts measurement accuracy. This improves quality assurance in offsite building. With a good Quality Management System (QMS), projects can save money and make clients happier.
Benefits of Quality Assurance | Results |
---|---|
Reduced errors in construction | 30% reduction |
Increased efficiency in problem-solving | 25% increase |
Improved client satisfaction | 70% of companies report improvement |
Learn About The Future of Sustainable Architecture: Net-Zero Buildings
Technology Integration in Modern Modular Buildings
Modular buildings are changing fast with new technology. This tech makes building offsite more efficient and better quality. Digital design tools, automation, and robotics are key. They help builders save money and time.
Studies show modular construction can cut costs by up to 20%. It also shortens building time by 20% to 50%.
Building Information Modeling (BIM) is a big part of this change. It gives a clear view of projects before they start. This makes planning much better. BIM uses 3D models instead of 2D blueprints, cutting down on waste.
Other new methods like 3D printing and augmented reality are also used. They help make designs more flexible and easier to see.
- Builds are better because there are fewer mistakes
- Designs can be more flexible, meeting more needs
- Robots and automation make building faster and more precise
- Delivery routes are better planned, thanks to GPS and sensors
The demand for modular buildings is rising. This is thanks to big investments like the U.S. Infrastructure Bill. Technology will be key in the future of building offsite.
The global modular construction market is expected to hit $214.76 billion by 2034. Digital tools, automation, and robotics will be vital for meeting this demand. They ensure buildings are efficient, sustainable, and of high quality.
Supply Chain Optimization for Construction Offsite
Effective supply chain management is key for construction offsite projects. It involves material procurement strategies and logistics management.
This ensures all parts are delivered on time and in good shape. The construction offsite industry is growing fast, with the U.S.
modular construction market valued at $10.53 billion in 2022. It’s expected to grow at 7.8% annually until 2030.
A good offsite construction plan lowers the risk of missing parts or storage problems onsite. Important logistics planning steps include setting timelines and organizing the supply chain.
Using Autonomous Mod Trailers helps make delivery routes more efficient, saving time and boosting transportation efficiency.
Material Procurement Strategies
Material procurement for off-site construction is complex. Each part needs specific design and is made only after orders are received.
This affects lead times. Contractors can’t keep large stockpiles because of the weight and bulk of construction parts.
Logistics Management
Good supply chain management means tracking materials and ensuring they arrive on time and in good condition. This avoids costly delays.
Real-time GPS tracking and advanced delivery monitoring software help with automated alerts on delays. Building strong relationships with suppliers is key to meeting project timelines.
Effective supply chain optimization strategies help construction offsite projects save money, improve quality, and work more efficiently.
This is vital in the construction industry, which is a big source of greenhouse gas emissions and energy use.
By using offsite manufacturing and modular construction, the industry can reduce its environmental impact while boosting productivity and efficiency.
Regulatory Compliance and Industry Standards
Off-site construction, like prefabricated and modular building, follows strict rules and standards. In the U.S., 35 states have their own rules for off-site parts.
Local areas handle specific site tasks. Using third-party agencies helps with inspections without needing state officials to visit.
The International Code Council (ICC) and Modular Building Institute (MBI) have set standards. These include ICC/MBI Standard 1200-2021 and ICC/MBI Standard 1205-2021.
These standards help meet building code rules and ensure consistency in off-site construction.
Compliance is shown through state labels and third-party inspection labels. A data plate also shows code and design details.
Key aspects of off-site construction standards include:
- State and local inspections
- Third-party plan review and inspection agencies
- Compliance with building code requirements
- Use of accredited third-party inspection agencies
New standards, like ICC/MBI Standard 1210, are being developed. It will cover Mechanical, Electrical, Plumbing Systems, Energy Efficiency, and Water Conservation in Off-Site Construction.
The committee is focusing on MEP systems, code compliance, and manufacturer instructions.
Standard | Description |
---|---|
ICC/MBI Standard 1200-2021 | Provides criteria for planning, design, fabrication, and inspection processes for off-site construction |
ICC/MBI Standard 1205-2021 | Provides criteria for the inspection and testing of off-site construction components |
ICC/MBI Standard 1210 | Focuses on Mechanical, Electrical, Plumbing Systems, Energy Efficiency, and Water Conservation in Off-Site Construction |
Conclusion: The Future of Construction Through Off-Site Innovation
The construction industry is changing fast, thanks to off-site construction, or modular construction and prefabricated building solutions.
These new ways of building promise better efficiency, quality, and sustainability. They are set to transform the sector in big ways.
Off-site construction is already making projects faster, cutting down timelines by over a third. Top builders are now delivering projects almost on time.
Digital tools and automation are making work safer and more efficient, while cutting down on waste.
Projects like the StepUp initiative show how off-site methods can help meet big goals. They aim to make buildings more energy-efficient and cut down on carbon emissions. This is key in the fight against climate change.
As people worry more about the environment, the need for green construction is growing. Off-site construction is becoming more popular for all kinds of projects.
The market for prefabricated buildings is expected to hit $130 billion by 2027. This could bring in more workers and help solve the problem of expensive housing.
FAQ
What is off-site construction?
Off-site construction, also known as prefabricated building or modular construction, is a way to build. It involves making a building or its parts in a controlled area away from the site. Then, these parts are moved and put together where the building will stand.
What are the key benefits of off-site construction?
Off-site construction offers many benefits. It improves quality control and cuts down on waste. It also makes construction faster and more efficient. Plus, it can save money and be better for the environment.
What are the different types of off-site construction?
There are two main types of off-site construction. Panelized construction involves making parts of the building off-site. Modular construction means making whole building modules off-site and then putting them together on-site.
How does off-site construction impact the economy?
Off-site construction can positively affect the economy. It lowers construction costs and boosts productivity. It also makes housing more affordable. This method can save a lot of money and make projects more efficient.
What are the essential components of modular construction systems?
Modular construction systems include structural parts, materials, and MEP systems. These are all designed and made off-site. This ensures quality and safety in the building.
How does off-site construction impact project timelines?
Off-site construction can make projects finish faster. It allows for work on multiple projects at once. This reduces the need for on-site labor, leading to quicker completion and better productivity.
What are the environmental benefits of remote construction?
Remote construction, or off-site construction, has big environmental benefits. It reduces carbon footprint and waste. It also uses sustainable materials, making projects more eco-friendly.
How is quality assured in off-site building methods?
Quality is key in off-site building. Strict quality control is used. This includes factory inspections and testing. It ensures the safety and quality of the building components and modules.
How is technology integrated into modern modular buildings?
Technology is vital in modern modular building. Digital design tools, automation, and project management software are used. These technologies enhance efficiency, quality, and productivity in off-site construction.
How is the supply chain optimized for construction off-site?
Optimizing the supply chain for off-site construction involves smart material procurement and logistics. This reduces costs, improves quality, and boosts efficiency in off-site construction projects.
What are the regulatory requirements for off-site construction?
Off-site construction projects must follow industry standards and regulations. This ensures the quality and safety of the final product. It includes meeting building codes and safety regulations.
- The Importance of Concrete in Construction
- Understanding the Properties of Concrete: A Comprehensive Guide
- Understanding the Key Properties of Concrete
- Exploring the Versatile Uses of Concrete in Everyday Life
- Understanding Concrete Classification: A Comprehensive Guide
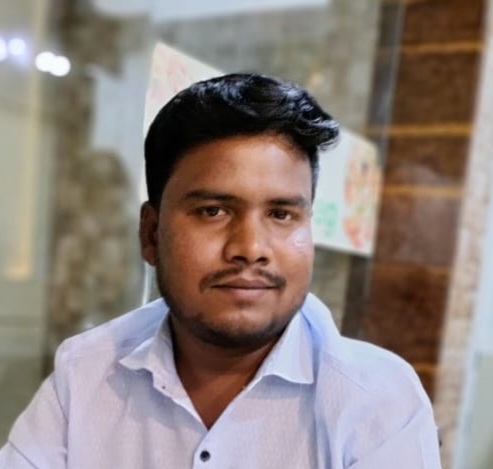
Author & Editor Of This Blog.
Founder Of “KPSTRUCTURES”