This Article Cover Details About Asphalt Batching Plant, Types Of Batching Plant And Components Of Asphalt Batching Plant.
Let’s Start With,
Introduction To Asphalt Batching Plant
An asphalt plant used for the manufacture of asphalt, macadam and other forms of coated road stone, sometimes collectively known as blacktop.
Asphalt Concrete mixes made with asphalt cement prepared at an asphalt mixing plant. Here, aggregates blended, heated, dried, and mixed with asphalt cement to produce a hot mix asphalt (HMA).
Types Of Asphalt Batching Plant
Asphalt Concrete plants are basically of two types, batch or drum mix.
- In the batch-type mixing plant, hot aggregate and asphalt withdrawn in desired amounts to make up one batch for mixing. After thoroughly mixing, the material discharged from the pugmill in one batch.
- In the drum-type mixing plant, the aggregate dried, heated, and mixed with the asphaltic cement in the drum in a continuous operation.
- Aggregate removed from storage in controlled amounts and passed through a dryer where it heated and dried. The aggregate then passes over a screening unit that separates the material into different size fractions and deposits them into bins for hot storage.er called a pugmill.
- Then the asphalt, which has also weighed, thoroughly mixed with the aggregate in the pugmill. After mixing, the material emptied from the pugmill in one batch.
Typical Asphalt Batching Plant

Batch Type Plant
- Cold aggregate feed
- Drying
- Screening
- Hot storage
- Measuring & mixing

Components Of Asphalt Batching Plant
- Cold Bins
- Dust Collector
- Cold Elevator
- Dryer Heater
- Cold Feed Gate
- Exhaust Stack
- Hot Elevator
- Screening Unit
- Hot Bins
- Weigh Box
- Mixing Bowl Or Pugmill
- Mineral Filler Storage
- Hot Bitumen Storage
- Bitumen Weigh Box

Cold Feed Supply
Cold aggregate feed is the first major component of the batch-type asphalt concrete plant. The cold feeder may charged by one or a combination of the following methods,
- Open top bins with two, three, or four compartments, usually fed by a crane with a clamshell bucket or a front-end loader.
- Tunnel under stockpiles separated by bulkheads. Materials stockpiled over the tunnel by belt conveyor, truck, crane, or front-end loader.
- Bunkers or large bins. These usually are fed by trucks, car unloaders, or bottom-dump freight cars, which empty directly into the bunkers.
When charging the cold feed, care should exercised to minimize segregation and degradation of the aggregate. This can prevented by taking the same precautions outlined for proper stockpiling.
Typical Three Bin Feed Cold System

Types Of Feeders And Controls
Aggregate feeder units are located beneath the storage bins or stockpiles, or in positions that assure a uniform flow of aggregate. Generally belt and vibratory feeders are best for accurate metering of the fine aggregates.
Coarse aggregates usually flow satisfactorily with any type of feeder. For a uniform output from the asphalt concrete plant, input must accurately measured.
There are several different types of cold feeders. Among the most common are,
- Continuous belt type (A)
- Vibratory type (B)

Lime Dispersion
When lime used in asphalt concrete, it must mixed by pugmill or other approved means to achieve a uniform lime coating on the aggregate prior to adding the asphalt cement to the mixture. The method of introducing and mixing the lime and aggregate shall be subject to approval by the Engineer prior to beginning production.
Dryer
- One of the basic units in any asphalt concrete plant is the dryer. It is a necessary part of the hot-mix operation for it dries and heats aggregates coming from the cold feed supply, thus making them suitable for mixing with asphalt.
- The dryer is usually a large rotating metal drum mounted at an angle and equipped with a gas or oil-heating unit at the lower end. Hot gases from the burner pass from the lower end of the rotating drum and out the upper end.
- Cold aggregate fed into the upper end of the dryer and picked up by steel angles or flights mounted on the inside of the unit. As the drum rotates, the aggregate lifted up and dumped through hot gases.
- Because of the inclination, the aggregate also gradually works its way toward the lower end of the dryer.
- The hot aggregate then discharges from the lower end onto a hot elevator that carries it to the screens and hot storage.
- Drying is the most expensive operation in mix production. It also the most frequently encountered bottleneck in the plant operation.
- The best dryer is the one that meets a desired performance level at the lowest investment and operating cost. Most dryers designed for average aggregate moisture content.
- Very wet aggregate will reduce the dryer capacity and require corrective measures.
Temperature Indicating Device
- Aggregate temperature measured by either a thermometer or a thermocouple attached to an indicating pyrometer. Pyrometers react much faster to changes in temperatures and usually preferred.
- An aggregate heat measuring device should installed in the dryer discharge in full view of the burner operator. This device is one of the most important plant control accessories and should be a reliable and accurate instrument.
- Overheating of the aggregate can damage the asphalt during mixing, under heating makes the aggregate difficult to coat with the asphalt and difficult to place.
DRYER WITH PRIMARY AND SECONDARY DUST COLLECTOR

Dust Collector
- The dust collector generally operated adjacent to and in conjunction with the dryer, and is necessary for efficient plant operation. The collector eliminates or abates the dust nuisance that might result from exhaust air from the dryer.
- Modern dust-collection systems are highly efficient. Provisions usually made in the dust collecting system to return the collected dust back to the hot aggregate as it emerges from the dryer and picked up by the hot elevator.
- If the collected dust unsuitable for use in the asphalt concrete mixture, it may removed from the collector and wasted. The dust collector fan(s) furnishes the draft that draws the flame and hot gases through the dryer.
- Dust particles from the dryer and other parts of the plant also carried in the current of draft air, which enters the dust collector at the upper periphery and goes into vertical motion.
- The heavier dust particles in the air stream separated by centrifugal force into the collector shell and fall to the bottom.
- The finer dust may remain in suspension and carried out the exhaust stack with the air.
- A wet wash system may added to the dust collecting system to reduce the amount of fine dust being carried out the exhaust stack with the air.
- There are several types of wet systems, but they all usually consist of a short tower, with or without baffles. Exhaust from the dust collector enters the tower at the bottom and passes upward through a series of water sprays that remove the dust.
- Use of a wet wash system usually will increase fan requirements by 10 to 15 percent because of the pressure loss in the tower.
Screening Unit
Dried aggregates generally transported from the dryer screening unit that is mounted over the plant bins. The function of hot screens is to accurately separate the aggregate into the specified sizes. the effective screening area must be large enough.
The condition and cleanliness of the screens will, control their efficiency. Excessive wear of the screen wire causes enlarged openings resulting in oversize material.

Hot Bins
- Hot bins used to temporarily store heated and screened aggregate in the various size fractions required. Each bin should be large enough.
- The overflow vents should checked frequently to make sure that they are free flowing and thus preventing contamination by intermingling from adjacent bins.
Aggregate Weigh Hopper
- Aggregates released from the hot bins into the weigh hopper, generally beginning with the largest size aggregate and progressing down to the finest size.
- Before withdrawal starts, there should always be sufficient materials in the hot bins for a complete batch.
Asphalt Bucket And Meter
- Asphalt may weighed in a special bucket, or by a meter for each batch., asphalt pumped into a bucket of known weight and weighed on a scale.
- The volume of asphalt changes with temperature. Some asphalt meters have built in temperature-compensating devices that correct the flow of asphalt when changes in temperature occur.
Truck And Plant Scales
Scales used in the weighing of materials paid for on a tonnage basis shall approved and sealed in accordance with the requirements of the policies of the Bureau of Weights and Measures of the Department of Agriculture and Consumer Services, or other approved agencies.
Asphalt Storage
- Asphalt storage at the plant should be equal to one day’s output.
- All storage tanks, transfer lines, pumps, and weigh buckets should have heating coils or jackets to maintain the asphalt at the required temperature.
Pugmill
A pugmill-type mixer commonly used in all modern asphalt concrete plants. This unit mounted directly beneath the weigh box and asphalt bucket.
Mixing
- The aggregates drawn from the hot bins.
- The wet mixing time begins with the start of the flow of asphalt from the bucket or meter.
- The dry mixing time should not be less than 15 seconds. However, the wet mixing cycle shall not be less than 20 seconds.
- Upon completion of the mixing time, the bottom of the pugmill mixer opens up and discharges the contents into a truck or other hauling equipment.

Automated Plants
Modern batch plants fall into three categories, depending on the degree of automation,
- Manual
- Semi-automatic
- Automatic
Drum Mix Plant
Drum mixing is a relatively simple process of producing asphalt mixtures.
The mixing drum looks like the familiar dryer, The difference that the aggregate not only dried and heated within the drum but also mixed with the asphalt cement.

Drum Mix Plant Components
The fundamental components of the drum mix plant are,
- Aggregate cold-feed bins
- Conveyor and aggregate weighing system
- Drum mixer
- Dust collection system
- Hot mix conveyor
- Mix surge bin
- Control van
- Binder storage tank

Safety
- Dust is particularly hazardous. Dust is not only a threat to lungs and eyes, but may contribute to poor visibility, especially when trucks, front-end loaders, or other equipment are working around the stockpiles or cold bins.
- Reduced visibility in work traffic is a prime cause of accidents.
- Noise may be a double hazard. Noise is harmful to hearing and may distract workers’ awareness of moving equipment or other dangers.
- Moving belts transporting aggregates and belts to motors and sprocket and chain drives are also hazardous. All pulleys, belts and drive mechanisms required to covered or otherwise protected.
- Loose clothing that may get caught in machinery never worn at a plant.
Thank You For Visiting…
Also Check Video Tutorial Site KPSTRUCTURES.COM
- Exploring the Advantages of Aggregate Materials in Construction
- The Advantages of Aggregate: Why It Matters in Construction and Beyond
- Exploring the Versatile Uses of Aggregate in Various Industries
- Understanding the Different Types of Aggregate: A Comprehensive Guide
- Understanding the Different Types of Aggregate in Construction
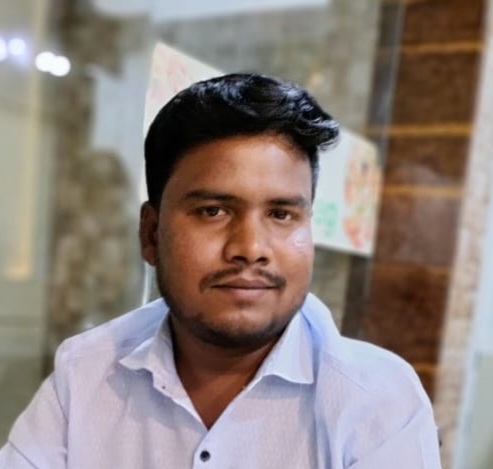
Author & Editor Of This Blog.
Founder Of “KPSTRUCTURES”
2 thoughts on “Asphalt Batching Plant 5-Type And 14-Components (2024)”