This Article Covers Bituminous Mix Design Their Requirements And Dry, Marshall Mix Design One By One.
Bituminous Mix Design
The bituminous mix design aims to determine the proportion of bitumen, filler, fine aggregates,
and coarse aggregates to produce a mix which is workable, strong, durable and economical.
The requirements of the mix design and the two major stages of the mix design, i.e dry mix design
and wet mix design.
Objectives of mix design
- Sufficient bitumen to ensure a durable pavement,
- Sufficient strength to resist shear deformation under traffic at higher temperature,
- Then Sufficient air voids in the compacted bitumen to allow for additional compaction by traffic,
- Sufficient workability to permit easy placement without segregation,
- Sufficient flexibility to avoid premature cracking due to repeated bending by traffic,and
- And Sufficient flexibility at low temperature to prevent shrinkage cracks.
Constituents of a mix
- Coarse aggregates
- Fine aggregates
- Filler
- Binder
Types of mix
- Well-graded mix
- Gap-graded mix
- Open-graded mix
- Unbounded
Different layers in a pavement
- Bituminous base course
- Bituminous binder course
- Asphaltic/Bituminous concrete
Requirements of Bituminous mixes
Stability
Stability is defined as the resistance of the paving mix to deformation under traffic load. Two examples of failure are
- Shoving – a transverse rigid deformation which occurs at areas subject to severe acceleration
- Grooving – longitudinal ridging due to channelization of traffic. Stability depend on the inter-particle friction, primarily of the aggregates and the cohesion offered by the bitumen.
Durability
Durability is defined as the resistance of the mix against weathering and abrasive actions.
- Pot-holes, – deterioration of pavements locally and
- Stripping, lost of binder from the aggregates and aggregates are exposed.
Flexibility
Flexibility is a measure of the level of bending strength needed to counteract traffic load and prevent cracking of surface. Fracture is the cracks formed on the surface (hairline-cracks, alligator cracks), main reasons are shrinkage and brittleness of the binder.
Skid resistance
It is the resistance of the finished pavement against skidding which depends on the surface texture and bitumen content. It is an important factor in high speed traffic.
Workability
Workability is the ease with which the mix can be laid and compacted, and formed to the required condition and shape.
Desirable properties
From the above discussion, the desirable properties of a bituminous mix can be summarized as follows:
- Stability to meet traffic demand
- Bitumen content to ensure proper binding and water proofing
- Voids to accommodate compaction due to traffic
- Flexibility to meet traffic loads, esp. in cold season
- Sufficient workability for construction
- Economical mix
Dry Mix Design
The objective of dry mix design is to determine the amount of various sizes of mineral aggregates to use to get a mix of maximum density. The dry mix design involves three important steps, viz. selection of aggregates, aggregates gradation, and proportion of aggregates, which are
Selection of aggregates
The desirable qualities of a bituminous paving mixture are dependent to a considerable degree on the nature of the aggregates used. Aggregates are classified as coarse, fine, and filler.
The function of the coarse aggregates in contributing to the stability of a bituminous paving mixture is largely due to interlocking and frictional resistance of adjacent particles.
Aggregate gradation
The properties of the bituminous mix including the density and stability are very much dependent on the aggregates and their grain size distribution.
However, some minimum amount of void space is necessary to :-
- Provide adequate volume for the binder to occupy,
- Promote rapid drainage, and
- Provide resistance to frost action for base and sub base courses.
Proportioning of aggregates
After selecting the aggregates and their gradation, proportioning of aggregates has to be done and following are the common methods of proportioning of aggregates:
- Trial and error procedure
- Graphical Methods
- Analytical Method
Marshall Mix Design
The mix design (wetmix) determines the optimum bitumen content. This is preceded by the dry mix design.
Marshall mix design
The Marshall stability and flow test provides the performance prediction measure for the Marshall mix design method. The stability portion of the test measures the maximum load supported by the test specimen at a loading rate of 50.8 mm/minute.
Specimen preparation
Determine the properties of the mix
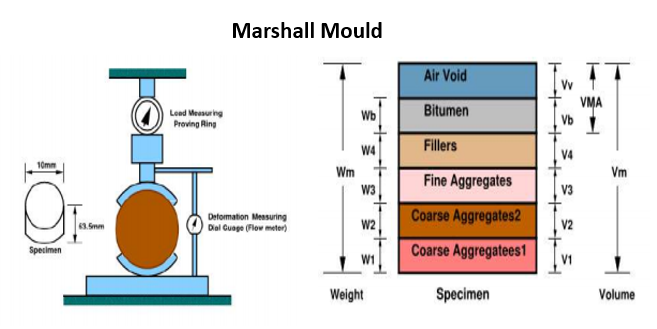
Theoretical specific gravity of the mix Gt
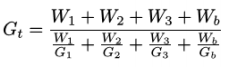
Bulk specific gravity of mix Gm
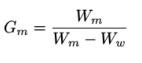
Air voids percent Vv
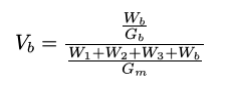
Voids in mineral aggregate VMA

Voids filled with bitumen VFB
Determine Marshall stability and flow
Marshall stability of a test specimen is the maximum load required to produce failure when the specimen is preheated to a prescribed temperature placed in a special test head and the load is applied at a constant strain (5 cm per minute).
Apply stability correction
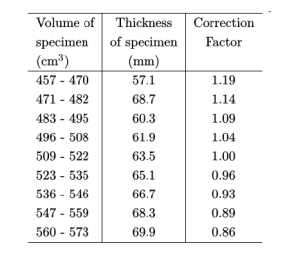
Prepare graphical plots
The average value of the above properties are determined for each mix with different bitumen content and the following graphical plots are prepared:
- Binder content versus corrected Marshall stability
- Binder content versus Marshall flow
- And Binder content versus percentage of void in the total mix v
- Binder content versus voids filled with bitumen (V F B) 5. Binder content versus unit weight or bulk specific gravity
Determine optimum bitumen content
Determine the optimum binder content for the mix design by taking average value of the following three bitumen contents found form the graphs obtained in the previous step.
- Binder content corresponding to maximum stability
- Binder content corresponding to maximum bulk specific gravity
- And Binder content corresponding to the median of designed limits of percent air voids in the total mix v (i.e. 4%)
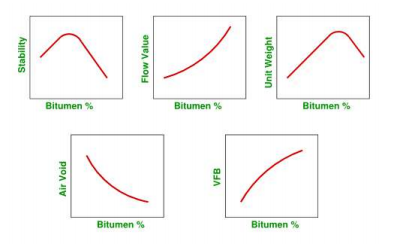
Thank You For Visiting…
Also Check Video Tutorial Site KPSTRUCTURES.COM
- What is framed structure?
- What is load bearing wall?
- What is earthquake load?
- What is wind load?
- What is live load?
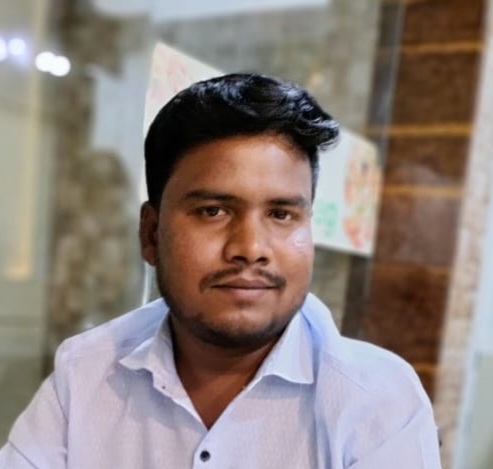
Author & Editor Of This Blog.
Founder Of “KPSTRUCTURES”
1 thought on “Bituminous Mix Design Dry And Marshall Mix Design”